I. Introduction to Euro Car Body
Euro Car Body (ECB) European Automotive Body Conference is hosted by Automotive Circle International (the world's leading automotive and supply chain communication platform), attracting technicians from complete vehicles, components, raw materials and research institutions from around the world. . It is held in Germany every October and the 15th in 2013.
The conference gathered global body experts to design, platform, modularize, new materials , weight and light weight factors, body structure connection, modal and stiffness, NVH, collision safety performance for this year's listed or upcoming models. As well as the production process, plant layout and maintenance convenience, etc., the evaluation and evaluation, and the vote of the participants, selected the best model of the year. The world's major automakers have taken the opportunity to analyze the latest technology in the research industry. This conference is also known as the world's largest and most public body BenchMark research conference.
Second, 2012 ECB (Euro Car Body) summary
The following picture shows the winners of the 2012 model participation.
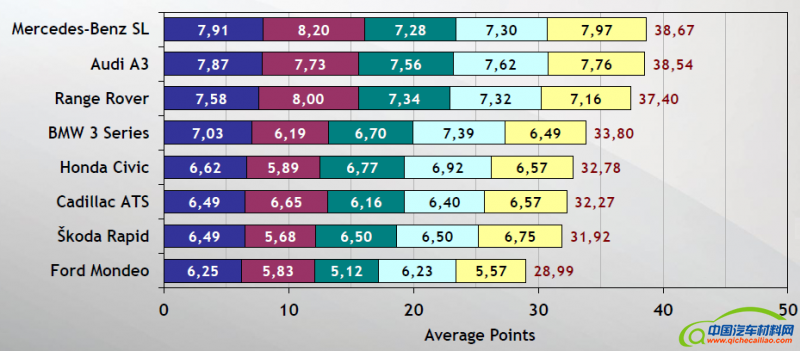
Detailed analysis of each model can view past records of the website:
2012 Euro Car Body Mondeo body material analysis
2012 Euro Car Body Cadillac ATS body material analysis
2012Euro Car Body Honda CIVIC body material analysis
2012 Euro Car Body new BMW 3 Series body material analysis
2012 Euro Car Body third-hand model - new Land Rover Range Rover body material analysis
2012 Euro Car Body runner-up - Audi A3 body material analysis
2012 Euro Car Body exhibits model material analysis (1) - champion model Benz SL
Each model has its own characteristics. The author makes a brief summary of the 2012 ECB from the aspects of body material distribution, new materials and new processes, structural design and lightweight engineering, so that readers can analyze and compare the latest ECB development in 2013. .
2.1 Body material distribution
Material distribution of steel body
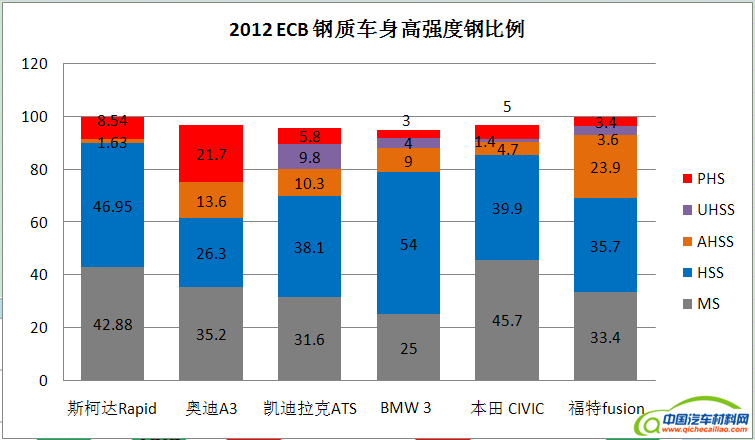
ECB's body high-strength steel application ratio is classified according to metallurgy type, not yield strength (see the high-strength steel application manual V4.1 for detailed classification), and the proportion of high-strength steel is up to 70%. The domestic high-strength steel application ratio is generally based on the yield strength (≥210MPa). If classified according to the high-strength steel of ECB, the domestic high-strength steel can reach nearly 70%, but domestic high-strength steel is mainly concentrated in yielding 210-340MPa. Between the excess strength steel and the hot formed steel with a yield greater than 550 MPa, the amount is less. Due to the low dosage of ultra-high-strength cold forming, and the cost of hot-formed steel is not too high in the self-owned models due to the cost limitation, the weight of the self-owned vehicle is quite heavy, which is not conducive to cost control. The application of domestic high-strength steels, especially ultra-high-strength steels, is mainly reflected in the forming and welding technology. In addition, there are domestic suppliers' supporting resources, including raw material suppliers, parts suppliers and molds. The ability to be strengthened remains to be strengthened. Â
2.2 New materials and new process application highlights
1 ) Application of die-cast aluminum alloy in the body
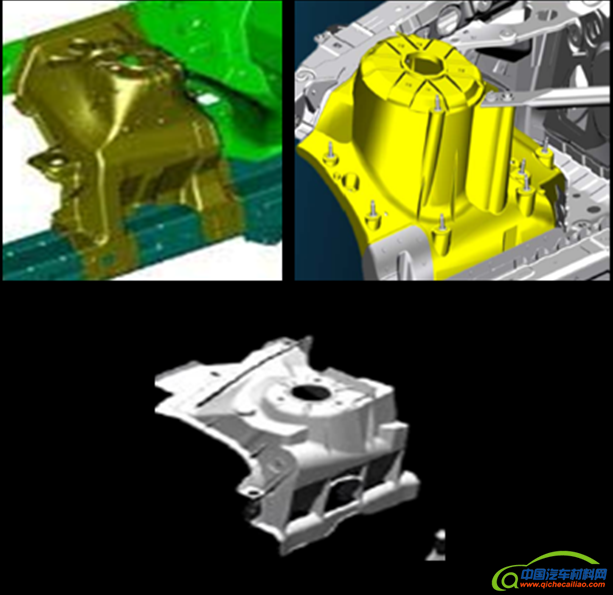
Deformed aluminum alloys have become quite common, but the use of die-cast aluminum alloys for large body parts such as the shock tower is still very challenging. Highly integrated and modularized, more than a dozen stamping parts can be integrated into one die-casting part; the die-casting process can improve the dimensional accuracy and reduce the cost of the mold; it can also solve the defects of the steel plate welding process at the shock absorber support. The fatigue failure problem and the improvement of the rigidity of the body. In addition to the application of the all-aluminum body to this technology, the Cadillac ATS steel body is also applied to this technology, which is indeed commendable. The obstacle to the application of self-owned brand products is not the cost, but the challenge brought by the new design concept. Â
2 ) Â FEM modular application is becoming a climate ( plastic or magnesium alloy)
This ECB has exhibited a total of 8 models, of which half of the modular FEM is applied. This technology has been widely accepted. It is not only used in high-end cars such as Land Rover and Mercedes-Benz. Many low-end Japanese and Korean cars sold in China are also used in large quantities, such as Hyundai Elantra. The enthusiasm for the development of independent brands is also very high. Jianghuai, Changan and Chery are developing, and Pentium has been applied in batches.
3 ) Hydroforming begins to be applied to body parts
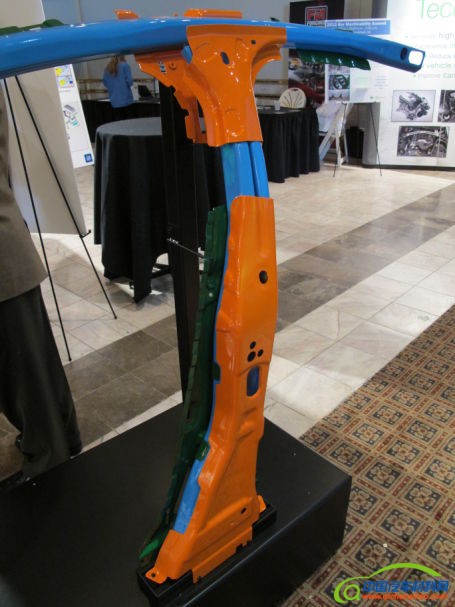
Hydroforming is very common on chassis components, but it is a bright spot on the body. The A- and B-pillars of the 2013 new Ford Mondeo are hydroformed. The use of hydraulic technology instead of the original thermoforming not only reduces weight, but also saves cost and materials. The most important point is better anti-collision performance. "Hydraulic forming technology makes the car body have better structural continuity. â€
“The tubular structure can help here, we maximize the cross-section of the column in the space that can be used. When the structure of the flange connecting the column is discarded, the vehicle will get better structural continuity, such as A The welded joint between the column and the roof rail. Due to the structure of the vehicle, it is not always possible to find a way to link the A-pillar to the roof rail."
When the independent brand is still considering whether the sub-frame should be hydroformed, others have already been used on the body; the application of hydroforming also shows that the rigidity of the tubular part is not completely replaced by the strength of thermoforming, so the car Performance is still "designed".
4 ) The amount of hot forming is high
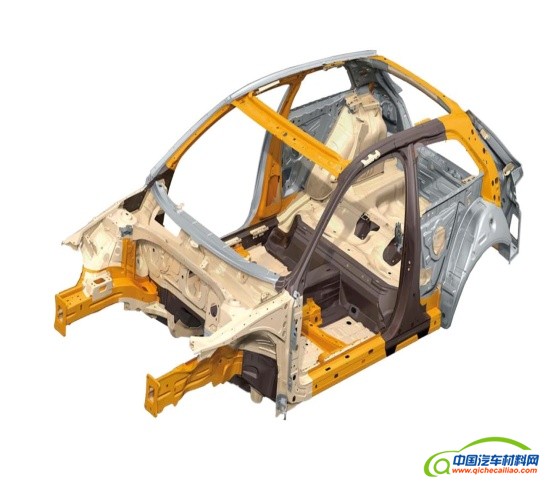
New audiA3 body thermoforming application
At present, the proportion of applications has increased year by year. At present, the most hot-formed models for industrialization are the latest audiA3, which is 21.7% of the weight of the car body, reaching 26.4% of the weight ratio of the body-in-white frame.
Trends and new technologies in thermoforming technology include thermoforming partial quenching, thermoforming TRB and thermoforming TWB.
5 ) Â New trend in differential plate application
TRB, also known as flexible rolled sheet, originated from Mubea in Germany. Domestic Baosteel defines it as VRB (Variable thickness Rolled Blank). Its application presents a trend of application in combination with thermoforming technology, taking advantage of its own advantages, achieving a combination of safety and light weight; of course, it can also be combined with hydroforming and roll forming. This kind of German-derived technology, Mercedes-Benz and BMW are the most widely used, and Ford is gradually applying it.
Audi A6 and A3 Â
6 ) Connection technology
In addition to traditional spot welding, ECB models also include arc welding, adhesive bonding, riveting, laser welding, stamping and self-tapping screw joining. The increase in the length of the bond and the equivalent number of solder joints contribute to the improvement of the rigidity and airtightness of the vehicle body (improvement of NVH), and there is still much room for improvement in this area.
At present, spot welding is the main in China, and cementation and arc welding are complementary. Only a few models have to use laser welding connections due to process realization problems. The connection of domestic body glue (including spot welding glue) is currently around 30-40m, and the length of pure structural glue is also in single digit (m), which is quite different from foreign countries. Â
2.3 body weight factor
As the overall trend of the body weight factor of the participating models in each year is declining; according to the propaganda materials of the relevant OEMs, the current body weight reduction coefficient is generally above 4, preferably 3.63. Â
2.4 Body structure highlight analysis
From the ECB material analysis, the Volvo, Audi, Honda and other OEMs actually designed the body structure from the experience level according to the ring structure characteristics. Wuhan Shangshan used the 3R-BODY design method to analyze the 2012ECB conference body.
1 ) Ring structure design
Judging from this year's ECB report, the mainframe plants that use the circular structure design idea to explain their body structure design are Audi and Honda, and they have followed their consistent lightweight design method.
2 ) Shotgun-Ring Evolution
Shotgun-Ring is a very important ring structure feature for the front structural body design. The design point is to connect the Shotgun with the front longitudinal beam. It is an important source of ideas for the pre-structure innovation design, from the Honda model Shotgun-Ring The importance of its contribution to performance can be seen in the evolution process.
Third, 2013 ECB new materials and new technology prospects
According to the ECB conference official website, the 2013 ECB reference models include Alfa Romeo 4C, BMW i3, Chevrolet Corvette, Ford Transit, Honda Fit, Infiniti Q50, Lamborghini Evando, Lexus IS, Mercedes S-Class, Opel Cascada, Land Rover Range Rover Sport Edition. It can be seen that this year, except for Honda Fit, which is a popular model, the other basics belong to sports cars, electric cars, luxury SUVs, etc., and the reference significance for the development of independent brand models is limited. Since the beginning of this year, this site has also collected relevant reports on the materials used in the above models. For details, please click:
2014 Corvette uses hydraulically formed stringers
BMW carbon fiber body structure analysis
Interpretation of carbon fiber BMW i3 electric vehicle material technology
The new generation of Honda Fit uses a rotating front seat
BMW i3 wants to reduce the weight of electric vehicles to the extreme
Extremely lightweight Alfa Romeo builds 4C bikes
2014 Lexus IS spy photos exposure will use all aluminum frame Â
If the all-aluminum body (Luohu new Range Rover), the new high-forming hot forming (Audi A3) and the new hydroforming application (Ford Mondeo) are the highlights of the new materials and new processes of the 2012 ECB. It can be predicted that: 2013 ECB new materials and new processes will continue the all-aluminum body (Land Rover Sport Edition), hydroforming (Chevrolet Corvette), the biggest highlight of this session will be: carbon fiber composite industry Application solution (BMW i3)! In addition, Alfa Romeo 4C and Lamborghini Evanta also use a large number of carbon fiber composites.
The author boldly predicted: no accident, the BMW i3 will receive the champion model of this session. Mainly due to its carbon fiber industry application, and the design of the all- composite body structure subverts the design concept of traditional metal (steel or aluminum) body (structural strength, forming, joining technology, painting and assembly, etc.), the system shows The new energy body structure design method will surely lead the trend of new energy vehicle body design.
In addition, today's traditional automotive technology gap is shrinking, low-cost, platform and modular automotive product design and production methods have received more and more attention, such as Volkswagen's MQB platform technology. Unfortunately, the public did not attend this meeting and did not have the opportunity to appreciate the public's interpretation of their MQB platform, but there is no doubt that this is an irreversible and important trend.
The ECB meeting provides domestic automotive technicians with an opportunity to get close to the most advanced international body structure and materials. From the whole industry, we should thank CITIC Metal for granting financial support to major companies over the years, so that engineers can go abroad and learn more advanced foreign technologies and concepts. I would also like to thank the Automotive Engineering Society and the Automotive Lightweight Alliance for setting up an industry communication platform for domestic body design and materials, and making important contributions to improving the technology of independent brands.
Flower Printed Fabric,Popular Printed Fabric,Delicate Colors Printed Fabric,Reusable Printed Fabric
SHAOXING HONEST IMP&EXP.CO.,LTD , https://www.transfer-printed.com