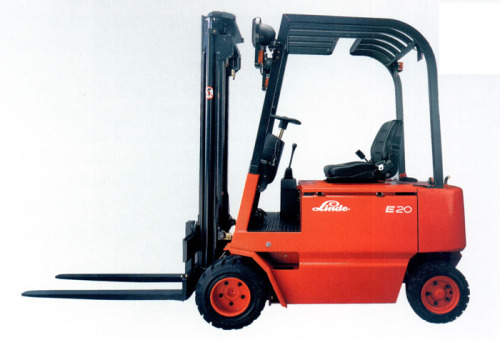
In 2012, the sales of motorized industrial vehicles in each month were as follows: In 2012, a total of 208,629 sets of internal-combustion-balanced heavy-lift trucks were sold, which was a decrease of 9.17% compared with 229,691 units in the same period of 2011. The number of electric forklifts (including electric counterbalanced heavy-duty forklifts and various types of electric storage forklifts) was 80033 units, which was a decrease of 0.58% compared with 80498 units in the same period of 2011. The number of electric warehouse forklifts was 50,124 units, which was a decrease of 0.76% compared with 50,508 units in the same period of 2011.
In the domestic market, a total of 212,958 mobile industrial vehicles were sold in the year, an increase of 9.04% compared with 234,115 in 2011.
In 2012, the number of motorized industrial vehicles exported was 75,704, a decrease of 0.5% compared with 76,074 units in 2011; among them, 29,892 were exported to electric forklifts, which was a decrease of 0.77% compared with the export volume of 32,379 units in 2011; the internal combustion forklift The number of exports (including container forklift trucks) was 45,812, an increase of 4.84% compared with the export volume of 43,695 units in 2011.
The overall decline in the sales of industrial vehicles in 2012 was mainly due to the slowdown in domestic economic development leading to a drop in demand. The economic recovery rate of the world's major economies was slow. The developing countries with strong demand in the previous two years also entered the adjustment period. These causes caused Domestic market and export pressures. It is expected that domestic and international demand for orders will improve in 2013. The growth of the industrial vehicle market will be around 5%, and the overall performance will show a steady and slowly rising trend.
Description
The Resin Sand Casting equipment consists of shell core machine,core shooter,casting machine,advanced coated sand formula and manufacturing technique.
This sand casting process is suitable for the production of cars,tractors and hydraulic parts.The molding materials include copper,iron and steel.
The surface of the sand is covered with a layer of solid resin molding sand or core sand before molding and core making,called coated sand.It was the first thermosetting resin sand.The precoated sand casting is a kind of casting process to put the roughing sand,resin and curing agent into sandbox after mixing evenly,and then molding and core making in the mold,finally pouring after mold closing.
Features of Coated Sand Casting Process
- Adopting advanced resin sand casting technology,we can professionally produce various types of non-ferrous casting products with complex shape and high inherent quality.
- The precoated sand casting products have many advantages of high dimensional accuracy,small machining allowance and high smooth finish.
- Other characteristics of the non-ferrous casting products include pore-free,no voids,good heat stability,excellent thermal conductivity and low expansion.
- The sand casting process can meet the customer requirements of the comprehensive mechanical properties.
Application of Resin Sand Casting
The precoated sand casting is a molding method,which attaches sand or other refractory materials to the prefabricated master batch,forms a cavity by sintering,and than injected into the molten metal and cooling.The sand casting process is mainly used for producing artwork and complex castings with high precision,such as engine and pump valve.
Technical Process
The resin sand casting is to mix the powdery thermosetting phenolic resin with raw sand,and then solidify after heating.Now it uses thermoplastic phenolic resin and latent curing agent (like urotropine) with a lubricant (such as calcium stearate) to form coated sand by sand casting process.When heated the resin wrapped in the surface of the sand is melting,under the action of the methylene decomposed from the urotropine,the molten resin rapidly transforms the linear structure into body structure,thus making the coated and curing.The suitable equipment is hot core box molding machine.The waste sand regeneration can not use mechanical regenerative way,so it should be subjected to 700℃ high temperature melting.The regeneration cost is higher,but the expansion coefficient of the regenerated sand is small and the performance is better than new sand.
Resin Sand Casting
Resin Sand Casting, Resin Bonded Sand Casting
QINGYUN HUIHUANG EXACT CASTING CO.,LTD , http://www.sdhhcasting.com