â€
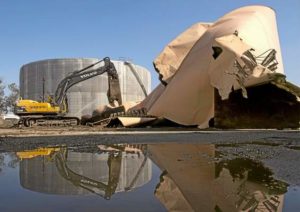
â€
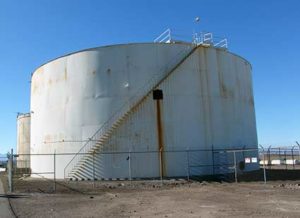
Revitalize Your Infrastructure: Avoid Costly Wastewater Tank Replacement
Replacing wastewater tanks can be a costly and disruptive process, involving extensive demolition, installation of new structures, and significant downtime. A recent article from the Whittier Daily News highlights Ridgeline Energy Services in Santa Fe Springs, CA, as they begin demolishing 19 aging tanks at their wastewater treatment facility. These tanks were part of the former Powerline Oil Co. refinery and had been plagued by odor issues due to wastewater mixing with residual sludge. Several leaks allowed hydrogen sulfide gas to escape through roof openings, affecting air quality but not posing a toxic risk. Each tank weighs 28 tons and holds up to 16,800 gallons of wastewater. The metal from the demolition will be recycled, and the solution for the odor problem involved removing and destroying the tanks rather than repairing them.
A Global Challenge
Ridgeline’s situation is just one example of a widespread issue. Over time, steel tanks can corrode and develop leaks. While temporary fixes like steel plates may stop leaks initially, these solutions often fail over time. A more sustainable alternative is using Carbon Fiber Reinforced Polymer (CFRP) technology, such as HJ3’s CarbonSeal systems. Full tank replacement not only costs millions in materials and labor but also has a major environmental impact—producing one ton of steel requires about 60,000 gallons of water. Replacing Ridgeline’s 19 tanks would have used around 32 million gallons of water. Repairing instead of replacing offers a smarter, greener option.
A Success Story: NRG Energy
HJ3’s CarbonSeal system proved to be a game-changer for NRG Energy, one of the largest power generation companies in the U.S. At one of its subsidiaries, a 2-million-gallon wastewater tank was leaking badly. Previous attempts with steel plates failed, leading to more problems, including thousands of through-holes in the walls and floor. The project required reinforcing the tank walls, floors, and support columns. During surface preparation and hydro-blasting, an additional 4,300 holes were discovered, which were then covered with steel plates. After that, HJ3’s CarbonSeal carbon fiber reinforcement system was applied to the entire structure. Surfaces were sandblasted, cleaned, inspected, and primed to prevent rust. High-modulus paste was applied, followed by the CarbonSeal system on walls, floors, and columns, all protected by a chemical-resistant topcoat.
A Sustainable Solution
By choosing to repair rather than replace, NRG extended the life of its tank by another 30 years. This decision saved the company millions in costs and significantly reduced its environmental footprint. Compared to full replacement, the project resulted in a 90% reduction in energy use, 96% less CO2 emissions, and saved 60 million gallons of water. NRG achieved savings of over $3 million, or 75%, by using HJ3’s CarbonSeal system. Whether you're facing similar challenges or seeking eco-friendly repair solutions, reaching out to our experts could make all the difference.
â€
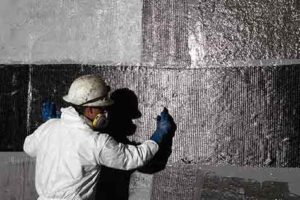
â€
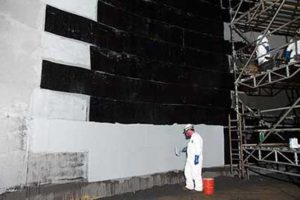
â€
Tin Making Machine,Metal Can Production Line,Tin Can Machine For Sale,Square Tin Making Machine Price
Zhoushan Golden Wing Machinery Co., Ltd. , https://www.goldenwingmachines.com